Lanthanum zirconate (chemical formula La₂Zr₂O₇) is a rare-earth oxide ceramic that has attracted growing attention for its exceptional thermal and chemical properties. This white, refractory powder (CAS No. 12031-48-0, MW 572.25) is chemically inert and insoluble in water or acid. Its stable pyrochlore crystal structure and high melting point (around 2680 °C) make it an outstanding thermal insulator. In fact, lanthanum zirconate is widely used for heat insulation and even sound insulation, as noted by materials suppliers. Its combination of low thermal conductivity and structural stability is also useful in catalysts and fluorescent (photoluminescent) materials, illustrating the material’s versatility.
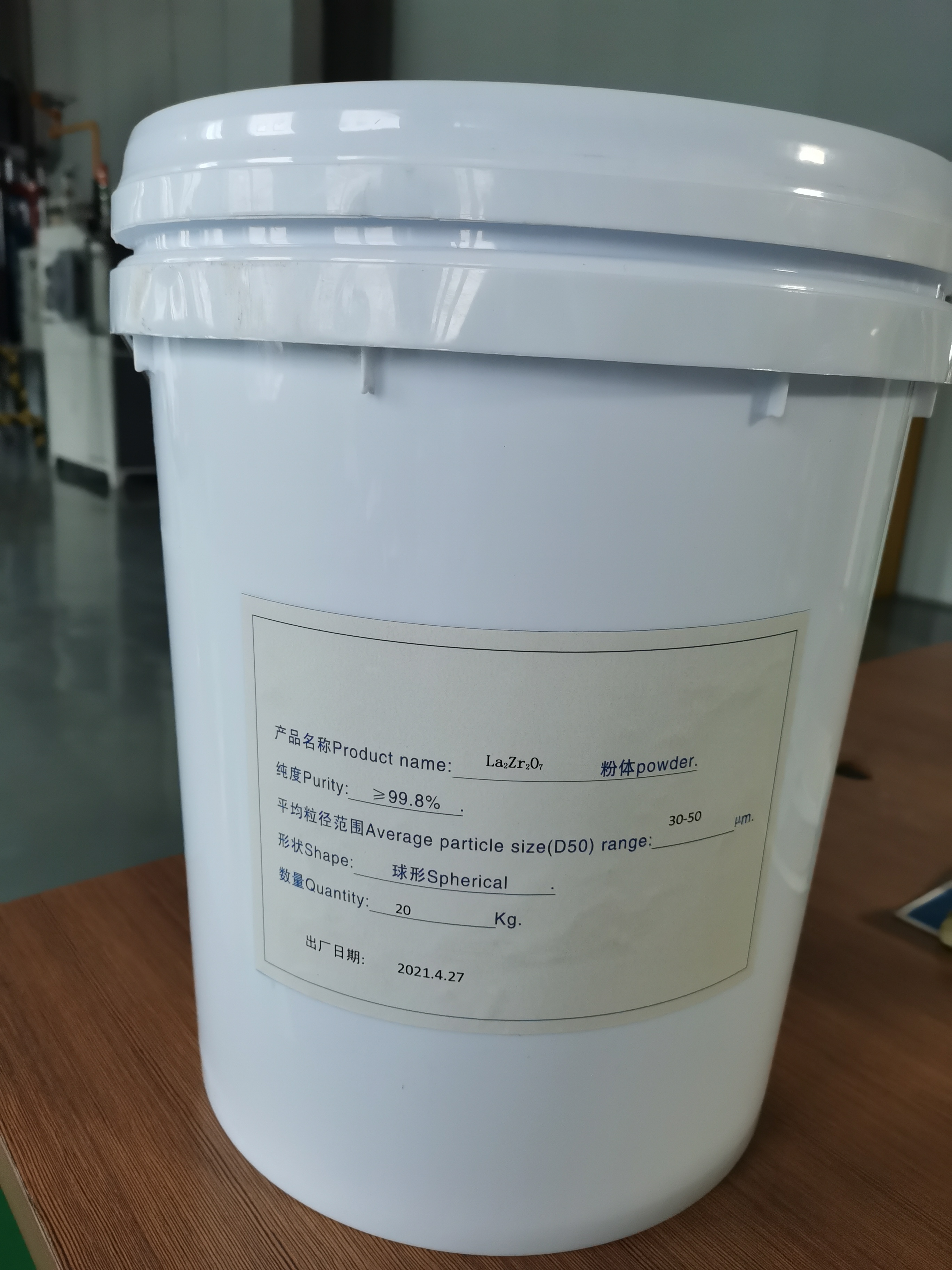
Today, interest in lanthanum zirconate is rising in cutting-edge fields. In aerospace and energy applications, for example, this advanced ceramic can help create lighter, more efficient engines and turbines. Its superb thermal-barrier performance means engines can run hotter without damage, improving fuel efficiency and reducing emissions. These traits also tie into global sustainability goals: better insulation and longer-lasting components can cut energy waste and lower greenhouse gas output in power generation and transportation. In short, lanthanum zirconate is poised as a high-tech green material that bridges advanced ceramics with clean-energy innovation.
Crystal Structure and Key Properties
Lanthanum zirconate belongs to the rare-earth zirconate family, with a general “A₂B₂O₇” pyrochlore structure (A = La, B = Zr). This crystal framework is inherently stable: LZO shows no phase transformation from room temperature up to its melting point. This means it does not crack or change structure under heat cycles, unlike some other ceramics. Its melting point is very high (~2680 °C), reflecting its thermal robustness.
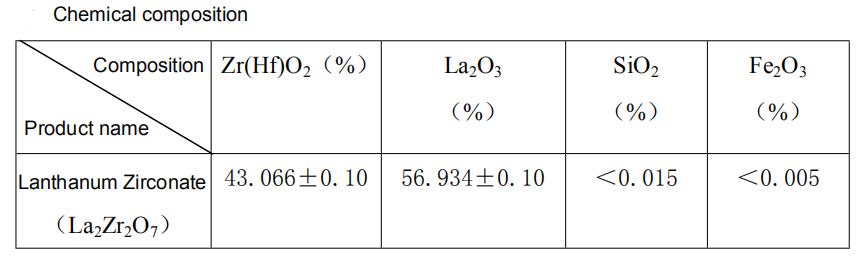
Key physical and thermal properties of La₂Zr₂O₇ include:
● Low thermal conductivity: LZO conducts heat very poorly. Dense La₂Zr₂O₇ has a thermal conductivity of only about 1.5–1.8 W·m⁻¹·K⁻¹ at 1000 °C. By comparison, conventional yttria-stabilized zirconia (YSZ) is much higher. This low conductivity is crucial for thermal barrier coatings (TBCs) that protect engine parts.
● High thermal expansion (CTE): Its coefficient of thermal expansion (~11×10⁻⁶ /K at 1000 °C) is relatively large. While a high CTE can cause mismatch stress with metal parts, careful engineering (bond coat design) can accommodate this.
● Sintering resistance: LZO resists densification at high temperatures. This “sintering resistance” helps the coating maintain a porous microstructure, which is essential for thermal insulation.
● Chemical stability: Lanthanum zirconate is chemically inert and shows excellent high-temperature oxidation resistance. It does not react or decompose easily in harsh environments, and its stable lanthanum and zirconium oxides are environmentally benign.
● Low oxygen diffusivity: Unlike YSZ, LZO has a low oxygen ion diffusivity. In a thermal barrier coating, this helps slow down oxidation of the underlying metal, extending component life.
These properties make lanthanum zirconate an exceptional heat-insulating ceramic. In fact, researchers highlight that LZO’s “very low thermal conductivity (1.5–1.8 W/m·K at 1000 °C for a fully dense material)” is a primary advantage for TBC applications. In practical coatings, the porosity can lower conductivity even further (sometimes under 1 W/m·K).
Synthesis and Material Forms
Lanthanum zirconate is typically prepared by mixing lanthanum oxide (La₂O₃) and zirconia (ZrO₂) at high temperatures. Common methods include solid-state reaction, sol-gel processing, and co-precipitation. Depending on the process, the resulting powder can be made very fine (nano- to micron-scale) or granulated. Manufacturers like EpoMaterial offer custom particle sizes: from nanometer powders to submicron or granulated particles, even spherical shapes. Purity is critical in high-performance applications; commercial LZO is available at 99.5–99.99% purity.
Because LZO is stable, the raw powder is easy to handle. It appears as a fine white dust (as seen in the product image below). The powder is stored dry and sealed to prevent any moisture adsorption, although it is insoluble in water and acids. These handling properties make it convenient for use in manufacturing advanced ceramics and coatings without special hazards.
Example of Material Form: EpoMaterial’s high-purity Lanthanum Zirconate (CAS 12031-48-0) is offered as a white powder tailored for thermal spray applications. It can be modified or doped with other ions to tune properties.
Lanthanum zirconate (La2Zr2O7, LZO) is a kind of rare-earth zirconate, and it is widely used in many fields as heat insulation, sound insulation, catalyst material, and fluorescent material.
Good Quality & Fast Delivery & Customization Service
Hotline: +8613524231522(WhatsApp&Wechat)
Email: sales@epomaterial.com
Applications in Plasma Spray and Thermal Barrier Coatings
One of the most important uses of lanthanum zirconate is as a topcoat in thermal barrier coatings (TBCs). TBCs are multilayer ceramic coatings applied to critical engine parts (like turbine blades) to insulate them from extreme heat. A typical TBC system has a metallic bond coat and a ceramic topcoat, which can be deposited by various methods such as air plasma spray (APS) or electron-beam PVD.
Lanthanum zirconate’s low thermal conductivity and stability make it a strong TBC candidate. Compared to conventional YSZ coatings, LZO can withstand higher temperatures with less heat flow into the metal. For this reason, many studies call lanthanum zirconate “a promising candidate material for TBC applications” due to its lower thermal conductivity and higher thermal stability. In plain terms, a lanthanum zirconate coating keeps hot gases out and protects the underlying structure even under extreme conditions.
The plasma spray process is especially suitable for La₂Zr₂O₇. In plasma spraying, LZO powder is heated in a plasma jet and propelled onto a surface to form a ceramic layer. This method creates a lamellar, porous microstructure that enhances insulation. According to the product literature, high-purity LZO powder is explicitly intended for “plasma thermal spraying (thermal barrier coating)”. The resulting coating can be tailored (e.g. with controlled porosity or doping) for specific engine or aerospace needs.
How TBCs improve aerospace and energy systems: By applying LZO-based coatings to engine parts, aircraft engines and gas turbines can safely operate at higher temperatures. This leads to more efficient combustion and power output. In practice, engineers have found that TBCs “retain warmth inside the burning chamber” and improve thermal efficiency while also reducing emissions. In other words, lanthanum zirconate coatings help keep heat where it’s needed (inside the chamber) and prevent heat loss, so engines use fuel more completely. This synergy between better insulation and cleaner combustion underpins LZO’s relevance to clean energy and sustainability.
Moreover, LZO’s durability extends maintenance intervals. Its resistance to sintering and oxidation means the ceramic layer stays intact through many heat cycles. A well-designed lanthanum zirconate TBC can therefore lower overall lifecycle emissions by reducing part replacements and downtime. In summary, plasma-sprayed LZO coatings are a key enabling technology for next-generation high-efficiency turbines and aero-engines.
Other Industrial Applications
Beyond plasma-sprayed TBCs, lanthanum zirconate’s unique properties find use in various advanced ceramics:
● Heat and Sound Insulation: As noted by manufacturers, LZO is used in general insulating materials. For example, porous lanthanum zirconate ceramics can block heat flow while also dampening sound. These insulating panels or fibres can be employed in furnace linings or architectural materials where high-temperature insulation is needed.
● Catalysis: Lanthanum oxides are known catalysts (e.g. in refining or pollution control), and LZO’s structure can host catalytic elements. In practice, LZO may be used as a support or component in catalysts for gas-phase reactions. Its stability at high temperature makes it attractive for processes like syngas conversion or automotive exhaust treatment, although specific examples of La₂Zr₂O₇ catalysts are still emerging in research.
● Optical and Fluorescent Materials: Interestingly, lanthanum zirconate can be doped with rare-earth ions to create phosphors or scintillators. The material’s name even appears in descriptions of fluorescent materials. For instance, doping LZO with cerium or europium could yield high-temperature-resistant luminescent crystals for lighting or display technologies. Its low phonon energy (due to oxide bonds) could make it useful in infrared or scintillation optics.
● Advanced Electronics: In some specialty applications, lanthanum zirconate films are studied as low-k (low dielectric) insulators or diffusion barriers in microelectronics. Its stability in oxidizing atmospheres and at high voltages (due to high bandgap) may offer benefits over conventional oxides in harsh electronic environments.
● Cutting Tools and Wear Parts: While less common, LZO’s hardness and thermal resistance mean it could be used as a hard protective coating on tools, similar to how other ceramic coatings are used for wear resistance.
The versatility of La₂Zr₂O₇ stems from it being a ceramic that combines rare-earth chemistry with the toughness of zirconia. It’s part of a broader trend of “rare-earth zirconate” ceramics (like gadolinium zirconate, ytterbium zirconate, etc.) that are engineered for niche high-temperature roles.
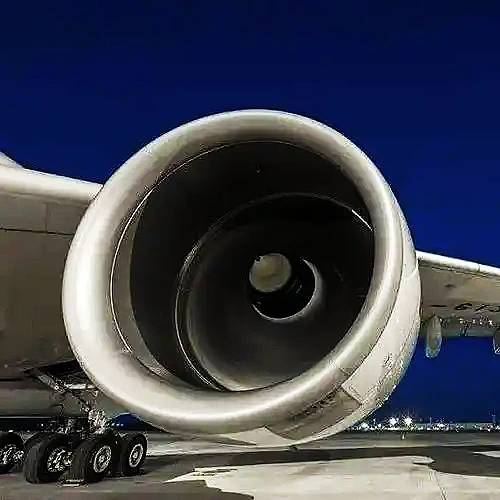
Environmental and Efficiency Benefits
Lanthanum zirconate contributes to sustainability primarily through energy efficiency and longevity. As a thermal insulator, it allows machines to achieve the same performance with less fuel. For example, coating a turbine blade with LZO can reduce heat leakage and thus improve the engine’s overall efficiency. Reduced fuel burn directly translates to lower CO₂ and NOₓ emissions per unit of power. In one recent study, applying LZO coatings in an internal combustion engine with biofuel achieved higher brake thermal efficiency and significantly cut carbon monoxide emissions. These improvements are precisely the kinds of gains sought in the drive toward cleaner transportation and energy systems.
The ceramic itself is chemically inert, which means it does not produce harmful by-products. Unlike organic insulators, it emits no volatile compounds at high temperature. In fact, its high-temperature stability even makes it suitable for emerging fuels and environments (e.g. hydrogen combustion). Any efficiency gains provided by LZO in turbines or generators amplify the sustainability benefits of clean fuels.
Longevity and reduced waste: LZO’s resistance to degradation (sintering and oxidation resistance) also means longer lifetimes for coated components. A turbine blade with a durable LZO topcoat may remain serviceable far longer than an uncoated one, reducing the need for replacements and thus saving materials and energy in the long run. This durability is an indirect environmental benefit, as less frequent manufacturing is required.
However, it is important to consider the rare-earth element aspect. Lanthanum is a rare earth, and like all such elements, its mining and disposal raise sustainability questions. If not managed properly, rare-earth extraction can cause environmental harm. Recent analyses note that lanthanum zirconate coatings “contain rare earth elements, which raise sustainability and toxicity concerns associated with rare earth mining and material disposal”. This underscores the need for responsible sourcing of La₂Zr₂O₇ and potential recycling strategies for spent coatings. Many companies in the advanced materials sector (including epomaterial suppliers) are mindful of this and emphasize purity and minimizing waste in production.
In summary, the net environmental impact of using lanthanum zirconate is generally positive when its efficiency and lifespan benefits are realized. By enabling cleaner combustion and longer-lasting equipment, LZO-based ceramics can help industries meet green energy targets. Responsible management of the material’s lifecycle is a key parallel consideration.
Future Outlook and Trends
Looking ahead, lanthanum zirconate is poised to grow in importance as advanced manufacturing and clean-tech continue to evolve:
● Next-Generation Turbines: As aircraft and power turbines push for higher operating temperatures (for efficiency or adaptation to alternative fuels), TBC materials like LZO will be critical. There is ongoing research into multi-layer coatings where a layer of lanthanum zirconate or doped LZO sits above a traditional YSZ layer, combining the best properties of each.
● Aerospace and Defense: The material’s radiation resistance (noted in some studies) could make it attractive for space or nuclear defense applications. Its stability under particle irradiation is an area of active investigation.
● Energy Conversion Devices: While LZO is not traditionally an electrolyte, some research explores related lanthanum-based materials in solid-oxide fuel cells and electrolysis cells. (Often, La₂Zr₂O₇ forms unintentionally at the interface of lanthanum cobaltite electrodes and YSZ electrolytes.) This indicates its compatibility with harsh electrochemical environments, which may inspire new designs for thermochemical reactors or heat exchangers.
● Materials Customization: The market demand for specialized ceramics is increasing. Suppliers now offer not only high-purity LZO but also ion-doped variants (for example, adding samarium, gadolinium, etc. to tweak the crystal lattice). EpoMaterial mentions the ability to produce “ion doping and modification” of lanthanum zirconate. Such doping can adjust properties like thermal expansion or conductivity, allowing engineers to tailor the ceramic for specific engineering constraints.
● Global Trends: With global emphasis on sustainability and advanced technology, materials like lanthanum zirconate will draw attention. Its role in enabling high-efficiency engines ties into fuel economy standards and clean energy regulations. Moreover, developments in 3D printing and ceramic processing may make it easier to shape LZO components or coatings in novel ways.
In essence, lanthanum zirconate exemplifies how traditional ceramic chemistry meets 21st-century needs. Its combination of rare-earth versatility and ceramic toughness is aligning it with fields that matter: sustainable aviation, power generation, and beyond. As research continues (see recent reviews on LZO-based TBCs), new applications will likely emerge, further cementing its importance in the advanced materials landscape.
Lanthanum zirconate (La₂Zr₂O₇) is a high-performance ceramic that brings together the best of rare-earth oxide chemistry and advanced thermal insulation. With its low thermal conductivity, high-temperature stability, and robust pyrochlore structure, it is particularly well-suited for plasma-sprayed thermal barrier coatings and other insulation applications. Its uses in aerospace TBCs and energy systems can improve efficiency and reduce emissions, contributing to sustainability goals. Manufacturers like EpoMaterial offer high-purity LZO powders specifically for these cutting-edge applications. As global industries push toward cleaner energy and smarter materials, lanthanum zirconate stands out as a technologically important ceramic — one that can help keep engines cooler, structures stronger, and systems greener.
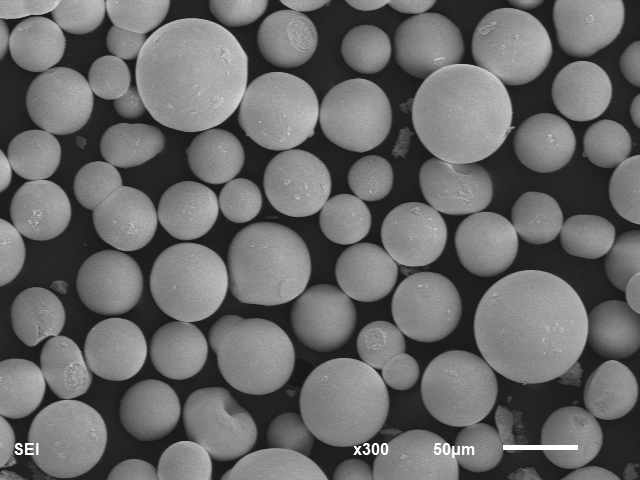
Post time: Jun-11-2025